Zinc Plating to Restore Plated Hardware
by Al Truax (First printed in the Morgan Plus 4 Club's Format)
When I examined the instruments on the 1954 Morgan that I'm restoring, I found the plated steel brackets that retain the speedometer, tachometer, and 4-1 gauges had lost nearly all the plating. They all had a uniform coating of rust and would need to be totally refinished.
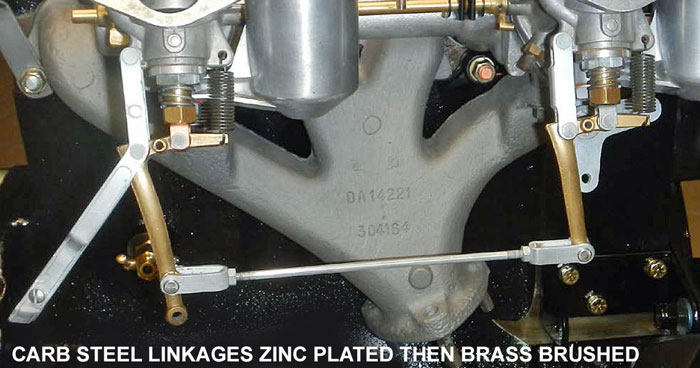
My options were either attempting to restore the original plating or painting them. I decided to try zinc plating to retain originality, but more importantly, to determine if that method was viable for home restoration of the many other rusted parts which were originally zinc plated.
1. Zinc Plating Bath Formulation
I started by researching plating solution formulas and found that most fell into three categories, those containing acids, caustics and/or cyanides. All formulations also contained a Zinc source and either sugars or proprietary mixtures to improve brightness and texture. I rejected any formulation that contained strong acids, strong bases, and most certainly all using cyanides. Several companies, notably Eastwood and Caswell, sell Zinc or Zinc-Tin plating kits for home use, marketing primarily to car restorers. I would consider these if a home brew method didn't provide satisfactory results.
I decided to first try the following recipe I found on a Ford Thunderbird website by Tom Gugliotta based on the availability of components, no proprietary ingredients, and low toxicity.
2. What is needed
300 grams epsom salts - (Magnesium Sulfate heptahydrate), (MgSO4-7H2O)
100 grams Zinc Sulfate monohydrate - (ZnSO4-H2O)
200 ml distilled white vinegar, 5% acidity
150 ml Karo brand light corn syrup
4 1/2 liters distilled or rain water
2 pure Zinc anodes
I found that I already had the epsom salts, vinegar and corn syrup, each can be found at grocery stores. The Zinc Sulfate and Zinc electrodes were purchased on Ebay for less than $20. (A recent price check on Ebay found 2 pounds of Zinc Sulfate for $8.99 and 4 Zinc anodes for $8.76 total cost with delivery.) While not particularly dangerous, Zinc Sulfate, plating solution and cleaning materials are irritants and can be poisonous if ingested. Disposable nitrile gloves and safety glasses should be used as a standard operating procedure when mixing or handling the plating solution or any chemicals.
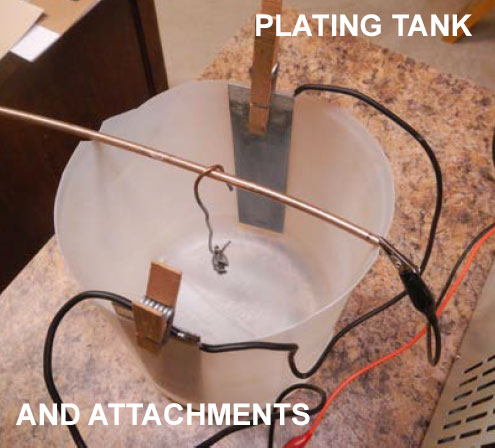
3. Plating Tank Set-up
I made a non-conductive plating tank by cutting the top off a plastic gallon jug. Any clean non-conductive container of suitable size and shape could be used and this was the right size and cost nothing. Two Zinc anodes were clamped to opposite sides of the tank with wooden clothes pins. The Zinc anodes were connected to the positive power source terminal and item to be plated is the cathode and connected to the negative terminal. It is desirable to have multiple anodes surrounding the work to help keep the plating thickness uniform. A length of 1/4" copper tubing was used as a support for hanging the item to be plated. The items were hung from the copper tubing by 12 gauge solid copper wire.
4. Power Source Requirements
Plating current control is important. A DC power source that is adjustable to control the plating current and an accurate means of measuring current such a digital VOM are required. The current settings for a quality Zinc plate depends on the surface area of the item to be plated so I tested the plating process to determine what current I needed. It is the current per square inch of plated surface and not the voltage that determines the quality and deposition rate of the plating. My online research indicated this current should be somewhere around 100 ma/square inch of surface area for the item to be plated. The 0-30 volt, 0-3 amp variable DC power supply I used was another
Ebay item that I purchased several years ago was ideal for the application. It has the ability to accurately regulate and read-out both current and voltage. As an alternative, a battery power source with a means of reducing the current to the required rate and a meter capable of measuring a small electrical currents could be used. Several of the items I plated required less than 100 ma and none required more than 1 ampere and never required more than two volts.
5. Determining the Plating Current
I cut a three square inch (1 1/2 square inch per side) sample of 22 gauge sheet steel to test the process and to determine the proper current to use to get a quality plate. With a current of 150 ma/square inch, the Zinc deposited quickly but was dark and was not uniform in texture. This dark appearance was barely perceptible near the sharp edges when
the current was reduced to 100 ma/square inch. I finally decided on
using a current of 80 ma/square inch which gave me a uniform bri
ght grey-white Zinc plate. Lowering the current below 80 ma/square inch did not appear to improve the results further. Only 0.9 volts was needed to achieve 80 ma/square inch with a sample of this size. I inspected the plated sample and found that the adhesion was excellent and that I was able to polish it to a bright metallic finish with a brass brush or with metal polish.
6. Preparing the Bracket for Plating
The steel retaining brackets were prepared for plating by bead blasting to remove all rust, then filing and sanding with wet & dry paper to remove defects. Any scratches or pitting left on the metal will be apparent after plating because the Zinc deposit will be too thin to conceal defects. The finish quality of the plated metal will be no better than the metal before plating. The metal must then be thoroughly cleaned before plating.
7. Plating Process
The prepared brackets were then dipped in a dilute acid bath for about minute to remove any flash rust that formed after cleaning, then dipped in rinse water and quickly placed in the plating tank. I used a dilute solution of PPG 579 metal cleaner for the acid dip. Use clean nitrile gloves when handling the parts for your protection and to ensure that the parts remain completely clean. I plated a bracket for 10 minutes at the calculated current of 80 ma/square inch and removed for inspection. I found a few tiny black dots where the surface did not plate properly. This was likely caused by rust pits to small to be seen that I thought I had polished out. I used a new clean fine abrasive pad to lightly buff the parts, briefly dipped in the acid bath, then rinse.