BUSH TYPES
by Lorne Goldman
1. PHOSPHER BRONZE (1909 to 2002)
2. PHOSPER BRONZE II (2006 - to date)
3. DEVOL (2001 to 2006)
4. VESCONITE (Non-Morgan Factory)
1. PHOSPHOR BRONZE I (1909 to 2002)
Morgan
has only used two bush materials in its long production history.
Phosphor bronze bushes are the original and current bush material, so we
have over 100 years of experience with it. It is an alloy of copper with
3.5 to 10% of tin and a significant phosphorus content of up to 1%. The
phosphorus plays the role of a deoxidizing agent during melting. The
product is known for its strength and its, low coefficient of friction.
It is also used for springs, bolts and various other items where
resistanceto fatigue, wear and chemical corrosion are required. It is, of course,
a dated materiel in the current world of amazing polymers.
In the days of mild steel
kingpins, (1909 to 2006) it resisted the wear caused by the quickly rusted surfaces these
kingpins..with a strength that turned out to be much durable than the later
experiments with softer, more modern materiels when used with mild steel
kingpins (up to 30,000 miles versus as little as 3000 miles with polymer
bushes like DEVOL). With non-rusting hard-chromed
kingpins,
used by cogniescenti for the last few decades, these bushes will achieve lift times of 100,000 miles. However, read this note.
2. PHOSPHOR BRONZE II (2006 to date)
These are the same as the Phospher Bronze I,
save that they have a spiral groove carved in their interior along with
a little "ring" of metal at one end. The latter feature began with the
DEVOL Morgans. This little ridge was hoped to act as A. a barrier to external grit entering and B. to keep the grease in. Of course when reamed or honed, the effect is prejudiced.
3. The DEVOL MORGANS (2001-2006)
by Lorne Goldman (6 updates since 2002)
At
the end of 2001, after a transition period of a few variations on the
theme, the Works removed the one-shot oiler system first installed in
the early 1950s and began using a new kingpin bush materiel rather than
the traditional phosphor bronze bushes used for almost a century. Many
have refer to them as plastic" or "neoprene" or "nylon" but, in fact,
they are not. They are Factory machined from a polyethylene plastic
called Devlon S made in Scotland by a company called Devol. They were
brought in to extend the notoriously short Morgan bush life AND to make
the task of bush installation easy rather than the involved task it is
now. Sadly, a number of factors and teething problems intervened,
giving these bushes an undeserved bad reputation. After approximately
2500 "Devol Morgans", the MMC abandoned the idea and returned to bronze
bushes. Subsequently, the MMC stopped supplying Devols and the Devol
cars must use oversize non-resultant fit bronze bushes, or make their
own out of Devol material.
The primary
cause of premature bush wear was never the bushes or the materiel used
for them..it was the use of mild steel kingpins. These will quickly
rust at the bottom bush when the car is stored for anything but a short
time. The exterior surface of the kingpins quickly becomes as rough and
acts like a rasp to grind through any materiel, especially the new
space-age materiels. Many moggers, myself included, had avoided this by
using hardchromed kingpins.
In 2002, right
after the first cars were fit with Devol, Bill Beck, a fine fellow and
(the last) full mechanical Morgan-familiar designer at the Factory left
their employ. By the 2003, reports were coming in from everywhere that
the bushes were lasting as little 3000 miles! A quick examination
showed the cause...rusting kingpins. They looked for a solution.
I was contacted
by the Factory by the director then in charge, Mark Aston. He wanted
input on hardchromes. They had reasoned out that any surface that does
not rust should solve the problem. We went back and forth for a month
or so. Sadly, for reasons explained here, in early 2004, the Company
moved from mild steel to stainless steel kingpins. This is an
ususual materiel to use in this application and there was no track
record for it.
Sadly, by 2006,
some owners were discovering that the kingpins were wearing faster than
the Devol! But by then Mark Aston had ceased working for the company as
well. I have been told by experts in the metal that the wear would
occur if the stainless bar stock chosen was of insufficent quality.
Hopefull this isue has been addressed since.
DEVOL'S RESULTANT FIT FEATURE
One super aspect
of these bushes is that were made to be a "resultant fit" meaning that
the bushes will automatically adapt to the correct ID once pressed into
the stub axles without the need for reaming or honing. They also can be
removed and inserted without the need for a multi-ton hydraulic press.
To make this possible, the Factory reamed the stub axle tube to a
standard ID. You when Morgan welds the kingpin tube onto the cast
stub axles, the ID varies from stub axle to stub axle as the high heat
from thes welding often distorts the tube.
Accordingly, the
specially machined and aligned tubes are found on all Devol cars. They
were a massively smart move, multiplying Morgan front end longevity and
making the dreaded front end job something any owner could perform on
his driveway. However, Morgan had problems. The DEVOL (or any modern
material is not as resistant as bronze (though bronze doesn't last very
long either). The older bushes method was invented long before the
charms of resultant fit was discovered.
OBSERVATION: Yes, even bronze can be made to be resultant fit if stub axle tubes are precisely machined.
This would be a smart move for all Miorgans as it would not change the
car's character, it would merely make it far more owner friendly. It would also go a long way to help the orphaned Devol car owners. |
Without
precision consistent stub axle tubes, each bush must be individually
fitted to each and every kingpin, which has always caused a long series
of woes to this day for all Morgan owners, new and old. Read on McDuff.
WATCHPOINT:
These bushes also have a tiny ridge on the ends. This ridge acts as a
barrier to grit and holds grease in. If reamed, this useful ridge is
removed. However, after Bill Beck left, some of the cars began
appearing with the bushes pressed in backwards with the little ridge
inside the tube.
|
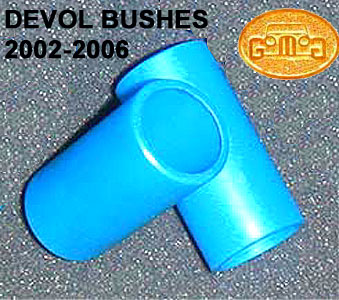 |
DEVOL SWELLING & SEIZING TALES
Most importantly, the Factory had an inconsistent experience with the
Devol bushes in the UK. This was self-caused but they did not
understand that at the time and, by that time, Bill Beck, the former
cheif designer had also left the company. The reaming of the stub axle
tube, and the bushes made by the factory from materiel supplied to
them, were both not made in a consistent size, id or od. At the time,
the Factory did not have the necessary machinery that could gurrantee
precision. They later bought a guided honer but this was well after the
Devol age. Also, after Bill Beck left, the production department
changed the amount they were reaming the stub axle tubes or bushes and
that changed the resultant clearance. Bill Beck originally called for
an ID of 1.24, the factory reduced to this to 1.2340 inches after his
departure..
So some Devol cars began seizing the kingpins when new. The Factory
blamed this on the Devol "swelling". Devol, a large interntional
company, responded to this writer that this was scientifically
impossible considering the the thicknesses and necessary clearances
involved. In any event, the MMC abandoned Devol and returned to bushes
made of the old phosphor bronze. The company will no longer
supply Devols bushes. If you want to keep them you must contact your
local Devol dealer in your country, get the bush material and have them
locally machined (any shop with a lathe). Or you must buy oversize
bronze bushes (because of their precisely machined, their kingpin tubes
are larger). Oversize bushes can be made at a local machine shop or
purchased from Mulfab.
WATCHPOINT aka Why so many new and rebuilt front ends seize: It
is interesting to note that some new cars have continued to have their
front ends seize, right from the Factory to this day (2016). They express this
with heavy steering, and/or steering that will not self-center easily.
And a very bumpy front end with an alarming amount of steering wheel
feedback where there should be none. This was exactly the characteristics
of the sadder Devol cars. New owners most often do not know what they are
experiencing, are most often too shy to investigate further as current
Morgan forums have conditioned them to believe that
"all-Morgans-do-that" and to do nothing. Should we now assume that bronze "swells" as well!!
But a practised Morgan person could diagnose
what has
happened to these cars with only these facts and with high probability.
The adage in such cases is a simple one. If you have problem
common to more than one car, eliminate anything they have that is
different from suspicion for your first analysis. (duh!) Devol
or their Devlon material has nothing in common with phosphor bronze.
What they do have in common here is that they are being used on the
same car and machined by the same persons. If the clearance machined
is insufficient, the front ends will seize whatever the material
or the expertise of the operator. In fact, these problems are more
common to the most experienced Morgan people, who have been doing this
job so long they don't both measuring any more.
The fact is that many practised machinists will machine Morgan bushes insufficiently. They not illogically feel that
creating too much clearance is effectively prematurely aging the
front end. They provide just enough clearance to allow the kingpins to
slip through the two, hopefully aligned bushes..often only 001-002" clearance. However, in
doing so, they have unwittingly provided no margin for the effect of the flexing Morgan chassis, the
degree of which varies from Morgan to Morgan, as it is effected by scores of
factors. With only minimal clearance, some cars, new or those with a rebuilt front end, must seize.
Some will not, which makes the culprit hard to finger.
If these symptoms appear with a new car or one that has a
newly rebuilt front, you must remove the front axles and increase the
bush/kingpin clearance to .004-005". The deceiving element about these seized cars is that if you jack them and remove
the weight from the front stub axles, they will most often seem perfect
with no detectable problem in steering or up-and-down movement! The reason for this is simple.
You have removed the effect of chassis flex. |
4. VESCONITE
Vesconite
and Vesconite Hilube are two bush materials developed in South Africa.
They are advertised as designed to operate with little or no greasing.
At the recommendation of a veteran and respected Morganeer, they have
been used by some moggers and replacements for phospher bronze and
suggested to the Factory, at one time, as a replacement for the DEVOLs.
They have been
tested and show less wear than bronze. But, with the use of hardchrome
kingpins, both will last beyond last a very long time. They do not
swell and they can even be used under water. They are ideal for dirty
or poorly lubriacted conditions. VESCONITE has high dimensional
stability and does not swell in water, in contrast to most synthetic
materials which swell in water. For example nylon absorbs up to 9%
water by weight with consequent swell and softening. They are ideal for
resultant fit axles.
I have used the regular Vesconite and had seizing issues. But I have been assured the Hilube is a problem-free choice by people I trust. I
now suspect the clearance on installation was insufficient even though
it was done by a famous Morgan professional. It is also hard to find
and expensive.
But from all accounts but mine, it is an excellent trustworthy product. However, the Factory is past the stage where this type of practical technology is of interest.